Why Logistics Centers Need High-Durability Marking Solutions for Warehouse Floor Marking? High-Traffic Areas?
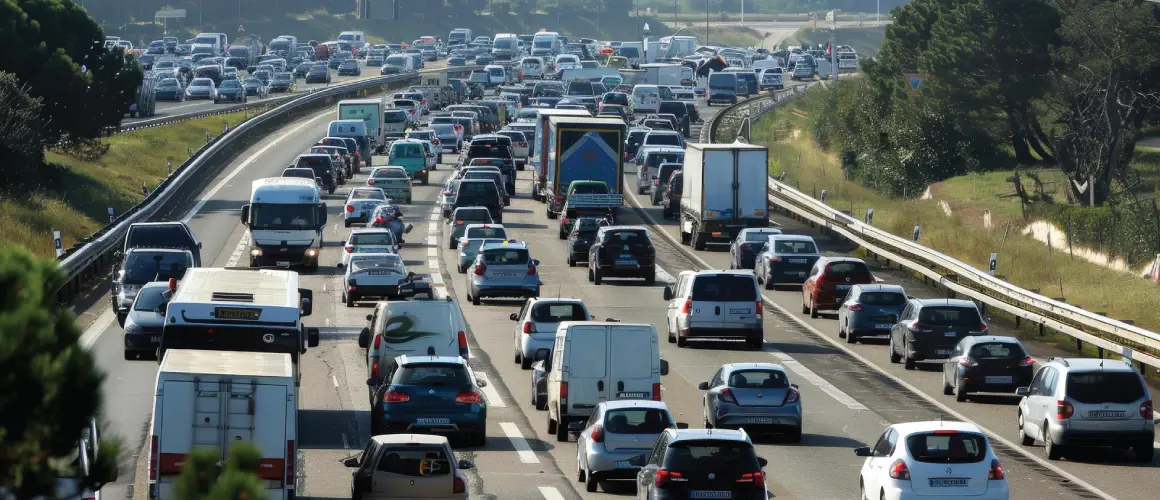
Yet, many facilities still rely on quick fixes—like budget paint or low-grade tape—that can’t withstand the pressure. These markings fade, peel, or get destroyed under foot traffic and forklifts within weeks. The result? Confusion on the floor, unsafe work zones, and unnecessary downtime. That’s why high-durability floor marking solutions are no longer optional—they’re essential infrastructure for any serious logistics operation.
Why is the logistics environment especially harsh on floor markings?
Logistics centers operate under relentless pressure—round-the-clock shifts, rapid goods movement, and strict schedules. Unlike standard industrial environments, warehouses in logistics facilities face a combination of mechanical wear, chemical exposure, and layout changes that put tremendous stress on floor markings. It’s not just foot traffic that causes deterioration; it’s the weight of loaded forklifts, constant turning wheels, oil drips, abrasive cleaning, and temperature changes that together wear down any surface marking that isn’t built for such intensity. Add to that the demand for quick reconfiguration in seasonal operations or e-commerce hubs, and it becomes clear why only the toughest marking systems survive. To understand why so many markings fail prematurely, you need to look at the real-world conditions they’re exposed to daily.
- Heavy traffic zones: Forklifts, tuggers, and pallet jacks pass over marked areas thousands of times a day. Standard tapes or paints simply can’t survive that level of friction.
- Aggressive cleaning routines: Floor scrubbers, degreasers, and chemical detergents are used daily. If the markings aren’t resistant to these cleaning agents, they fade fast or start flaking.
- Mixed-use areas: Some zones are constantly reconfigured for seasonal stock, while others (like dock doors or emergency paths) are fixed. This requires a mix of permanent and removable solutions—something basic materials can’t handle.
- Temperature and moisture variation: Some facilities include cold storage, while others face open dock exposure. Low-grade markings crack, blister, or delaminate under thermal stress.
Why are durable floor markings critical for warehouse safety standards?
In high-throughput logistics environments, safety isn’t just a policy—it’s a structural requirement. Floor markings help guide pedestrian movement, define restricted zones, and highlight hazards long before an incident occurs. But when those markings fade or become unclear, the safety system breaks down right at the foundation. In many cases, poor floor visibility is a contributing factor in warehouse accidents involving forklifts, spills, or congestion in shared zones.
Regulatory bodies such as OSHA, ANSI, and ISO have laid down specific requirements for warehouse safety markings, including color usage, width, reflectivity, and durability. Non-compliance isn’t just risky—it can lead to operational shutdowns or insurance complications after incidents. This makes high-durability markings not only a safety measure but a legal and functional necessity.
- Walkways must be clearly separated from vehicle lanes.
- Exit paths and emergency zones need to remain visible at all times.
- Safety colors (yellow, red, green) must retain their identity over time.
- Aisle markings should remain intact even under regular mechanical wear.
- Forklift charging areas must be visibly designated and unobstructed.
- Hazardous material zones require reinforced chemical-resistant coatings.
- Facilities with dim or night-shift operations benefit from photoluminescent marking systems.
How to choose the right warehouse floor marking solution for different zones?
Not all warehouse zones serve the same function—and treating them with a one-size-fits-all marking solution leads to premature failure, confusion on the floor, and higher maintenance costs. The best approach is to match the marking material and application method to each zone’s operational demands, traffic pattern, chemical exposure, and change frequency.
Permanent, high-impact areas like loading docks or forklift highways need materials that can survive years of friction and scrubbing, while flexible zones such as staging or modular racking layouts may benefit more from removable or repositionable markings. Environmental factors such as cold storage temperatures or chemical handling areas add another layer of complexity to the selection process. Here’s how to break it down:
- Heavy-use drive lanes and intersections:
These areas take the brunt of tire friction, weight loads, and turning traffic. Thermoplastic or solvent-resistant epoxy markings are recommended due to their high bond strength, abrasion resistance, and visibility under movement. - Cold storage and freezer zones:
Standard floor paints fail under low temperatures. Instead, use specially formulated epoxy coatings or methyl methacrylate (MMA) systems that can cure and bond even in sub-zero environments without cracking or lifting. - Racking aisles and shelving layouts:
These zones change frequently in many facilities, especially in e-commerce or FMCG warehouses. High-performance vinyl or PVC-based tapes offer quick application, easy removal, and minimal disruption during layout changes. - Battery charging, flammable storage, and chemical zones:
Markings in these areas must withstand chemical exposure, oil drips, and in some cases static buildup. Epoxies with chemical-resistant additives or grounding-compatible finishes work best here. - Staging areas, cross-docks, or inbound/outbound zones:
Markings in these locations often serve as visual indicators for truck bays, pallet organization, or time-sensitive stock. Using color-coded, UV-stable floor tapes helps maintain clarity even under heavy movement and variable lighting conditions.
What makes high-durability markings more cost-effective long term?
At first glance, high-durability markings seem more expensive. But when you calculate the full cost—including downtime, rework, and labor—they’re usually the smarter investment.
- Longer service intervals: While budget paint may last 3–6 months, a proper epoxy or thermoplastic line can go 3–5 years without needing touch-ups.
- Fewer shutdowns: Re-marking floors often means halting operations in that area. Longer-lasting solutions drastically reduce this frequency.
- Lower manpower use: Durable systems need fewer reapplications, meaning less reliance on contractors or in-house teams for maintenance.
- Better ROI: You’re not just saving on material—you’re preserving time, safety, and operational clarity. The payback often becomes clear within the first year.
Conclusion
Warehouse floor markings are much more than just lines on concrete—they’re safety systems, navigation aids, and operational boundaries rolled into one. And in logistics centers, these lines face more punishment than nearly any other surface.
That’s why high-durability marking solutions aren’t a luxury—they’re a necessity. Whether it’s epoxy for your main drive lanes, thermoplastics for your outdoor areas, or industrial tapes for your modular racking zones, choosing the right marking materials means smoother workflows, safer workers, and less money burned on rework.
Need help finding the right floor marking system for your warehouse? – Reach out to our team at info@aaspaequipment.com and we’ll help you pick the best-fit solution based on your facility type, workflow, and long-term goals.