Asphalt Drum Mix Plant
We are leading manufacturer and supplier of Asphalt Drum Mix Plant in Ahmedabad, India. Specifically created for the manufacturing of hot-mix asphalt used in road construction and maintenance, an asphalt drum mix plant is a vital part of the construction sector. This complex piece of equipment effectively blends bitumen, aggregates, and other necessary components to produce a consistent and long-lasting asphalt mixture. Drum mix machines operate constantly, unlike batch plants that manufacture asphalt in discrete batches, making them extremely efficient and perfect for large-scale projects.
The revolving drum, where aggregates are heated and combined with hot bitumen to create the asphalt mixture, is the center of an asphalt drum mix plant. High levels of automation and exact temperature and proportion control throughout the process guarantee consistency and high-quality results. These facilities are essential for the building and upkeep of roads, bridges, and other infrastructure projects because of their reputation for dependability, speed, and capacity to generate a wide variety of asphalt mixtures. An asphalt drum mix plant is a crucial instrument in contemporary building projects because it improves the smoothness of road surfaces, lowers maintenance costs, and increases motorist safety.
Aaspa Equipment’s Asphalt Counter Flow Drum Mix Plant – Delivering High-Performance Asphalt Mixing with Efficiency and Precision

Sub Heading
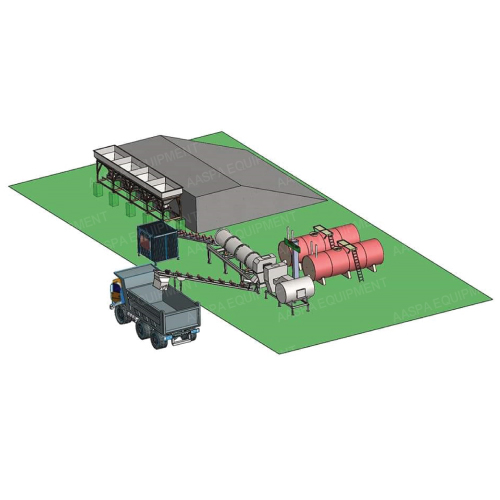
Sub Heading
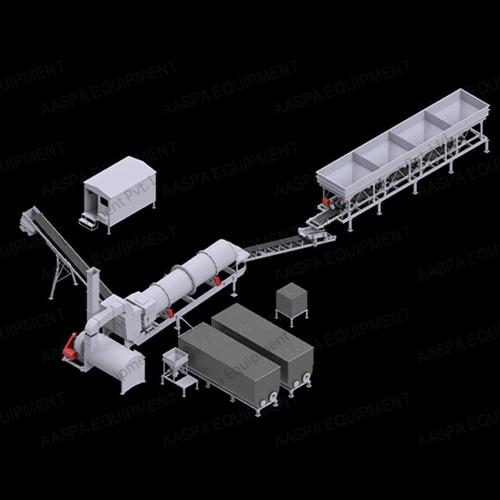
Sub Heading
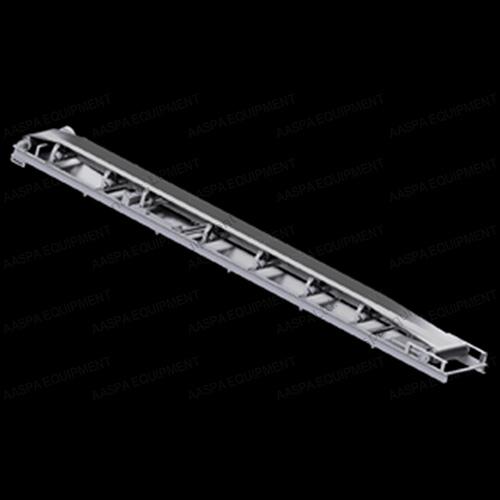
Sub Heading
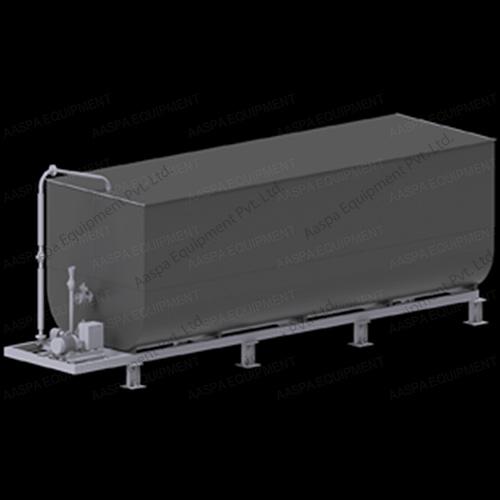
Sub Heading
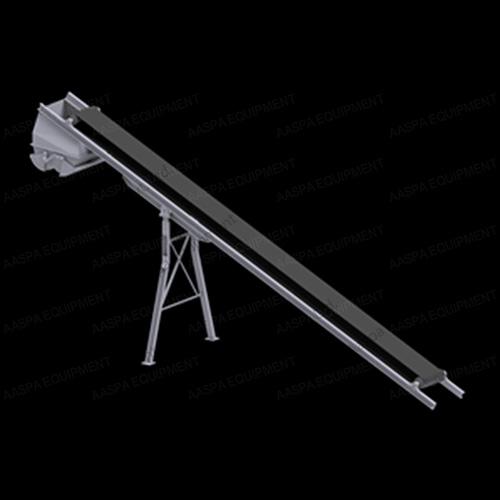
Sub Heading
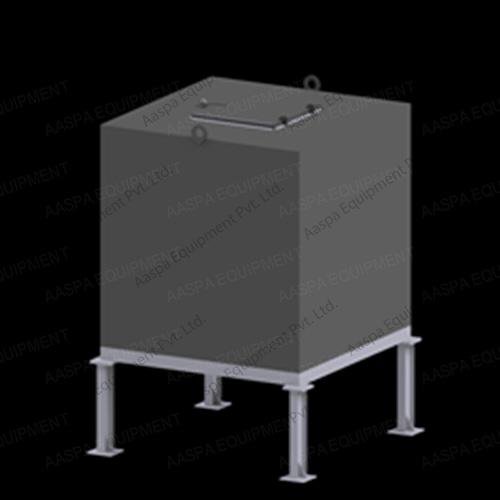
Sub Heading
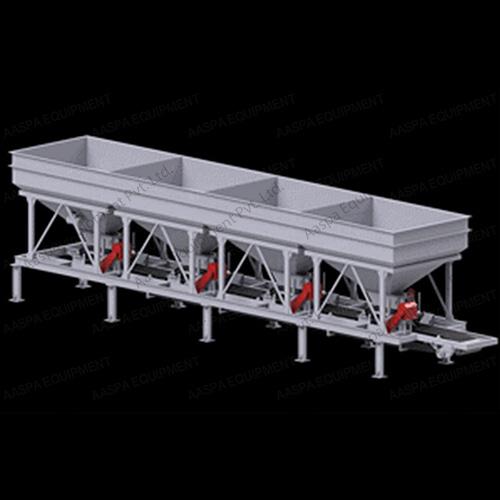
Sub Heading
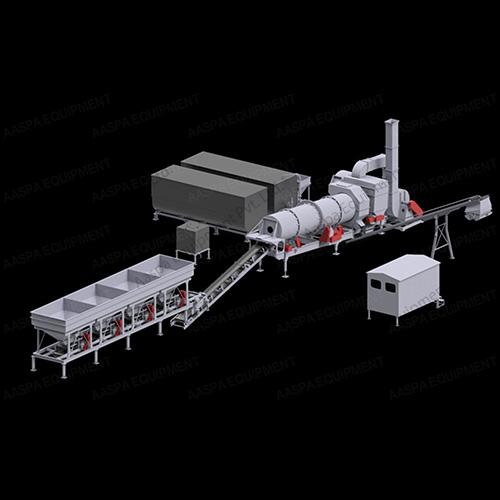
Sub Heading
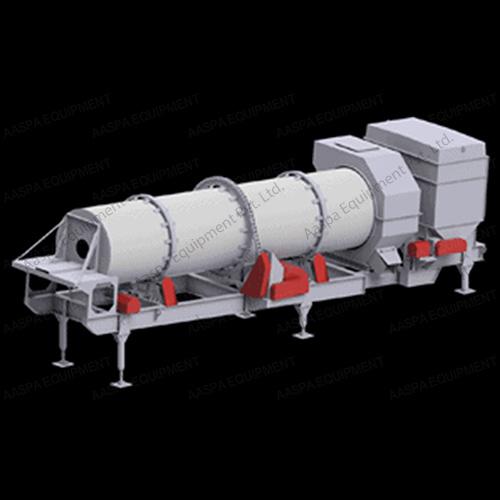
Sub Heading
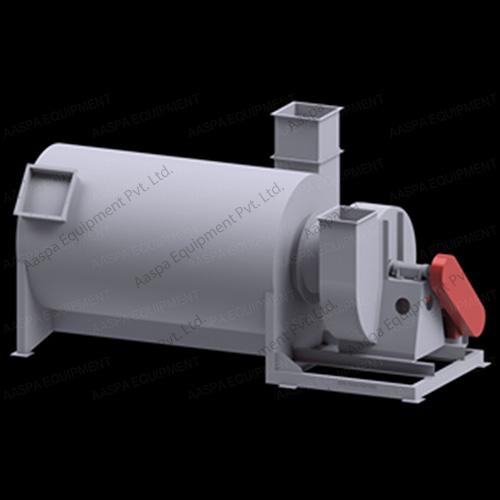
Sub Heading
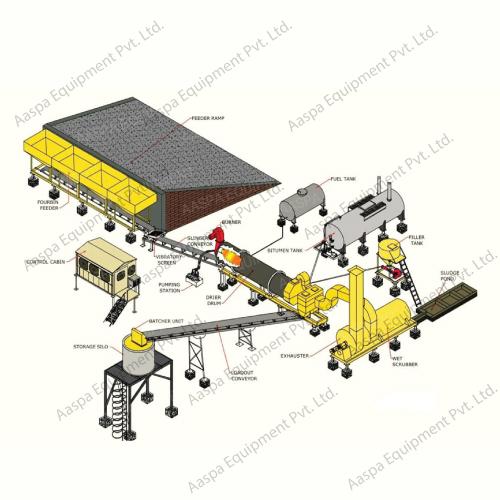
Sub Heading
Technical Specifications
MODEL | ADM – 20 | ADM – 35 | ADM – 45 | ADM – 50 | ADM – 60 | ADM – 90 |
CAPACITY RANGE (TPH)* | 15 to 20 | 30 to 45 | 45 to 60 | 60 to 90 | 90 to 120 | 120 to 150 |
DRYER | ||||||
Length (m) | 5 | 6.2 | 6.2 | 6.75 | 6.75 | 8.5 |
Diameter (m) | 1.05 | 1.13 | 1.22 | 1.5 | 1.02 | 2.1 |
Insulatin (Cerawool in mm) | 25 | 25 | 25 | 25 | 25 | 25 |
Exhauster (CFM) Burner | 5500 | 7500 | 10500 | 14500 | 18500 | 22500 |
Rating (Ltrs./Hr.) | 150 | 150 | 250 | 50 | 560 | 900 |
BIN FEEDER | ||||||
No of Bins | 4 | 4 | 4 | 4 | 4 | 4 |
Bin Capacity (MT) | 8 | 8 | 11 | 11 | 13 | 13 |
Belt Feeder width (mm) Gathering | 500 | 500 | 500 | 500 | 500 | 500 |
Conveyor width (mm) | 600 | 600 | 600 | 600 | 600 | 600 |
SLINGERCONVEYOR | ||||||
Conveyor Width (mm) | 600 | 600 | 600 | 600 | 600 | 600 |
LOADOUT CONVEYOR | ||||||
Conveyor width (mm) | 600 | 600 | 600 | 600 | 600 | 600 |
Loadout Height (m) | 3.2 | 3.2 | 3.2 | 3.2 | 3.2 | 3.2 |
Hopper Capacity (kg) | 800 | 800 | 800 | 1000 | 1000 | 1000 |
POWER REQUIREMENTS | ||||||
Drum Drive (HP) | 10 | 15 | 20 | 30 | 40 | 60 |
Exhauster (HP) | 10 | 15 | 20 | 25 | 50 | 75 |
Bin Feeder Hopper (HP) | 4 x 2 | 4 x 2 | 4 x 2 | 4 x 2 | 4 x 3 | 4 x 2 |
Gathering Conveyor (HP) | 3 | 5 | 5 | 5 | 7.5 | 7.5 |
Slinger Conveyor (HP) Vibratory | 3 | 5 | 5 | 5 | 7.5 | 7.5 |
Screen (HP) Loadout Conveyor | 1 | 1 | 1 | 1 | 2 | 2 |
(HP) Hydraulic Powerpack (HP) | 3 | 5 | 0 | 0 | 7.5 | 7.5 |
Bitumon (Asphalt) Pump (HP) | 2 | 2 | 2 | 2 | 5 | 5 |
FillerUnit | 3 | 3 | 3 | 3 | 3 | 5 |
Rotary Valve (HP) | – | – | – | – | – | – |
Blower (HP) | 1.5 | 1.5 | 2 | 2 | 5 | 5 |
Dryer Automatic Burner | 5 | 5 | 5 | 5 | 5 | 5 |
Fuel Pump (HP) | 2 | 2 | 2 | 2 | 3 | 5 |
Blower (HP) | 3 | 3 | 5 | 10 | 15 | 25 |
Hot Oil Pump (HP) | 0.5 | 0.5 | 0.5 | 0.5 | 0.5 | 0.5 |
BITUMEN TANK | ||||||
Capacity (MT) | 15 | 15 | 15 | 20 | 20 | 15 x2 |
Insulation (Glasswool in mm) | 50 | 50 | 50 | 50 | 50 | 50 |
FUELTANK | ||||||
Capacity (Ltrs.) | 2500 | 2500 | 5000 | 5000 | 5000 | 10000 |
TOTAL CONNECTED LOAD LOAD (KVA) | 80 | 100 | 120 | 135 | 220 | 300 |
- Easy Operation and Less maintenance.
- Designed for the International Market.
- Modern Drum Mix Technology.
- Proper Asphalt Coating and saving.
- Proper Drying and Homogeneous Mixing of Aggregate.
- Less Fuel Consumption.
- Continuous Electronic Belt weighing system with Load cell.
- SCADA / PLC based control panel with online print out facility.
- Schneider make HMI with touch screen.
- Easy to Operate
- Modular Design For Transport
- Completely Pre Wired Get set and Go
- No Civil Works Massive saving
- SCADA / PLC Based control Panel with online print out facility.
- Complete chassis with wheel Hub axle assembly in chassis with Drum Front rear break kaman patta Air tank landing gear king pin wheel rims, tyres.
Bitumen Heating & Storage Tanks
Fully insulated double walled tank is equipped with separated high – pressure electronic burner for heating the Asphalt and control unit capable of metering and spraying required quantity of bitumen at specified temperature.
The positive displacement jacketed Asphalt pump coupled with reduction gearbox and variable speed motor is provided with hot oil circulating system.
All the Asphalt carrying pipelines are hot oil jacketed and thoroughly Insulated with asbestos tape.
- External insulation with ceramic wool and covered with suitable thick sheet.
- Tested tube nest for diathermic oil circulation.
- Thermic duct, manhole, lifting hooks, breather pipe.
- Electronic high-pressure jet burner.
- Heavy duty jacketed Asphalt pump
- Thermometers.
Drum Machines
THERMO DRUM The drying and mixing unit of the asphalt plant demands complex flight design and heat transfer technology. With its continuous R & D and incorporation of the latest design up- gradations. Aaspa thermo drum is miles ahead of competition. The Aaspa thermo drum unit follows a triple heat transfer system that ensures a total transfer of heat to the aggregates translating into higher productivity and lower fuel consumption. The heat is transferred to the aggregates using the conductive, convective and radiation techniques. The unique flight design ensures total heat transfer, a through mixing & coating, lower emissions and prevention of bitumen oxidation
Burner
Thermo drum burner is the heart of the entire system hence its efficiency, ease of serviceabillity etc. are most important factors
- Two stage high & low
- Capacity to reduce the moisture up to 0.5% and achieve 180 Deg. Celsius for aggregate.
- Able to use LDO / FO / Diesel as fuel.
- Nozzle cleaning is possible during running condition.
- Fully automation operation.
Cold Aggregate Bin Feeder Unit
Discharge System
Fuel Storage Tank
Filler Storage Unit
Weighing System
Pollution Control Unit
Control System
A user Friendly software gives you total reliability and ensures top notch performance.
Fail proof power interlocks and auto process controls. Online fault detection, Online printing facility Provisions to print, store and edit production details, mix proportions. etc. Display of all process control parameters, Auto I manual operation. The control is equipped with function keys and numeric keys and does not require special skills for operation.