5 Key Maintenance Tips for Keeping Your Pothole Patcher Machine in Top Shape
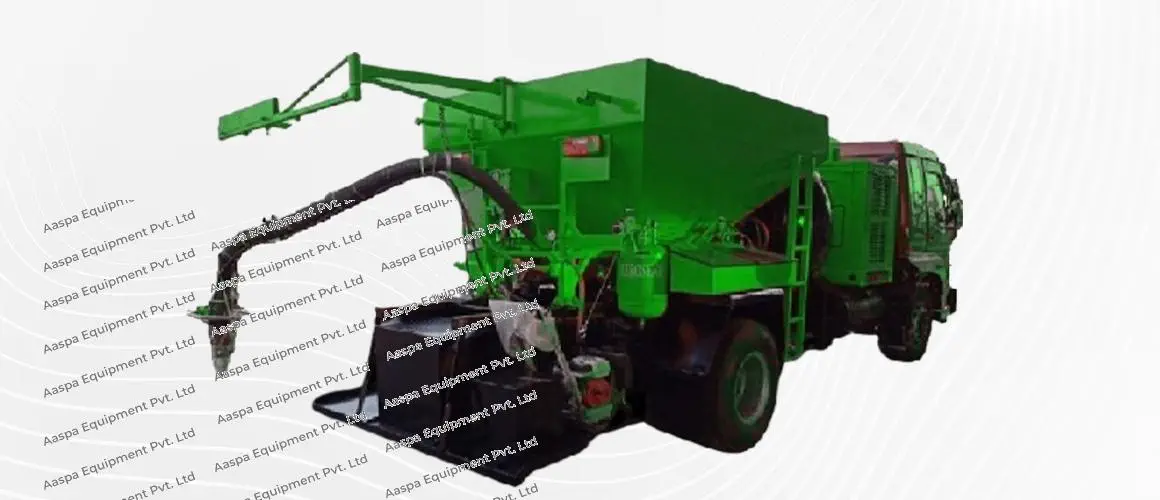
However, even the most advanced machines can falter without proper care. Routine wear and tear, overlooked inspections, and delayed servicing can drastically impact their performance and reliability. Regular, well-planned maintenance is the key to preserving their efficiency. With the right knowledge and approach, these machines can consistently perform at their best, saving time, resources, and unnecessary repair costs.
In this guide, we’ll explore practical maintenance tips, share insights to help you avoid common pitfalls, and outline steps to keep your pothole patcher machine running smoothly for years to come.
Why Proper Maintenance of Pothole Machines Matters?
Proper maintenance isn’t just about keeping a machine operational; it’s about preserving its ability to perform with precision and efficiency. A well-maintained pothole patcher ensures seamless repairs, reduces operational delays, and extends the lifespan of your investment.
Neglecting maintenance often leads to costly breakdowns, uneven repairs, and increased downtime. These setbacks not only inflate expenses but also compromise road safety and the overall quality of your projects.
- Avoid unexpected failures during critical operations.
- Minimize fuel consumption and operational costs.
- Ensure consistent and high-quality repairs.
- Reduce wear and tear on vital components.
- Prevent damage from residue buildup in heating and emulsion systems.
- Maximize machine life while maintaining reliability.
- Save on long-term repair and replacement expenses.
Common Challenges in Maintaining Pothole Patcher Machines
Keeping a pothole patcher in peak condition comes with its own set of hurdles. These machines handle heavy-duty tasks in challenging environments, making them prone to wear and tear. Without proactive care, even minor issues can snowball into costly problems, affecting efficiency and repair quality. Understanding these challenges is essential for implementing the right maintenance practices.
- Residue buildup in the emulsion delivery system affects bonding quality.
- Irregular lubrication leads to excessive wear on moving parts.
- Clogged or inefficient heating systems result in uneven asphalt temperatures.
- Leaks in hydraulic systems cause performance and pressure issues.
- Neglected inspections fail to catch minor issues before they escalate.
- Poor storage conditions accelerate corrosion and damage to critical components.
Key Maintenance Tips for Pothole Patcher Machine
1. Perform Daily Inspections
Regular inspections are your first line of defense against potential issues. Before starting operations each day, check for:
- Fluid Levels: Ensure that hydraulic fluid, engine oil, and coolant levels are adequate. Low levels can lead to overheating or system failure.
- Hoses and Fittings: Inspect for any visible signs of wear, cracks, or leaks in hoses and fittings. Leaks can disrupt performance and cause environmental hazards.
- Tire Pressure and Tread: Proper tire maintenance ensures smooth operation, especially when moving between job sites.
Spotting and addressing minor issues early can save you from costly repairs and downtime later.
2. Keep the Heating System Clean
The heating system in a pothole patcher is vital for maintaining the right temperature for the asphalt mix. A dirty or clogged heating system can result in uneven heating, leading to subpar repairs.
- Clean burners and heating elements regularly to prevent carbon buildup.
- Inspect insulation and seals to avoid heat loss.
- Test the temperature control system to ensure accurate heating of the mix.
Proper heating not only improves the quality of the repair but also enhances fuel efficiency.
3. Lubricate Moving Parts
Friction can wear down critical components over time, especially in a machine that handles heavy-duty tasks like pothole patching. Regular lubrication reduces wear and tear on parts like:
- Chains and sprockets
- Hinges and pivot points
- Augers or conveyors
Use manufacturer-recommended lubricants and follow the prescribed schedule to maintain optimal performance and extend the lifespan of your equipment.
4. Monitor the Emulsion Delivery System
The emulsion delivery system plays a pivotal role in ensuring the bonding agent is evenly applied. Issues in this system can lead to improper patching.
- Flush the system regularly to remove blockages caused by residue buildup.
- Inspect nozzles and hoses for clogs or leaks.
- Calibrate the spray system periodically to ensure accurate application.
- A well-maintained emulsion system ensures the repaired area is durable and long-lasting.
5. Follow a Preventive Maintenance Schedule
While daily checks are crucial, a comprehensive preventive maintenance schedule can address deeper issues and keep your machine in peak condition. This schedule should include:
- Engine Maintenance: Regular oil changes, filter replacements, and spark plug checks.
- Hydraulic System Check: Test pressures and inspect hydraulic lines for wear.
- Electrical System Inspection: Check the battery, wiring, and connections to ensure reliable operation.
Stick to the manufacturer’s recommended intervals for service and keep detailed maintenance logs. A structured approach minimizes unplanned downtime and ensures the machine is always ready for action.
Additional Tips for Enhancing Longevity of Pothole Patcher Machine
In addition to the above-mentioned core maintenance tips, there are several proactive measures that can help extend the lifespan of your pothole patcher machine. These tips complement your regular upkeep routine and ensure that the machine operates at its best, preventing minor issues from turning into major problems.
- Train Operators: Ensure operators are well-trained in using and maintaining the machine, reducing mishandling and avoidable wear and tear.
- Use Manufacturer-Approved Parts: Always replace worn components with parts recommended by the manufacturer to maintain efficiency and reliability.
- Protect Against Weather: Store the machine in a covered area or use protective covers to shield it from rain, heat, and frost, which can cause rust and degradation.
- Clean Key Components: Regularly remove asphalt and debris from exposed parts to avoid clogs and maintain smooth operation.
- Schedule Professional Inspections: Periodic inspections by professionals can uncover hidden issues and prevent major breakdowns.
- Avoid Overloading: Operate the machine within its recommended capacity to prevent stress on vital components and ensure long-term functionality.
- Maintain a Service Log: Keep a detailed record of all maintenance activities to track wear patterns and plan timely servicing effectively.
Noticing The Signs Saying “It’s Time for Professional Servicing”
Even with diligent maintenance, there are moments when professional intervention is needed. Watch out for:
- Excessive noise or vibrations during operation.
- Recurring performance issues despite regular upkeep.
- Sudden spikes in fuel or material consumption.
Seeking timely professional servicing can prevent further damage and restore your machine’s efficiency.
Final Verdict
Maintaining your pothole patcher machine doesn’t have to be a daunting task. With the right practices and a proactive approach, you can ensure that your equipment runs smoothly and efficiently, day in and day out. Regular inspections, proper lubrication, and timely servicing are key to maximizing its lifespan and performance. So, whether you’re tackling potholes in a busy city or working on remote roads, keeping your machine in top shape will save you time, money, and a lot of headaches down the line.
Got questions or need expert advice on maintaining your equipment? We’re here to help! Reach out to us at info@aaspaequipment.com, and let’s keep your pothole patcher running like new.