Top Maintenance Tips to Extend the Lifespan of Your Kerb Paver Machine
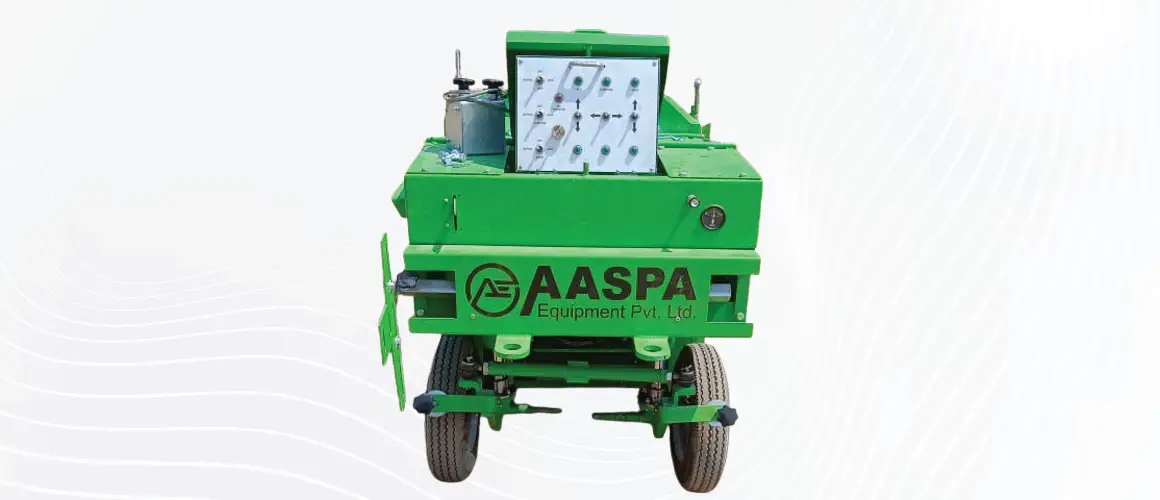
Proper kerb paver machine maintenance ensures optimal performance, prevents mechanical failures, and extends the operational lifespan of critical components. This article covers essential maintenance practices, key inspections, and additional strategies to enhance the durability of your kerb paver machine.
Why Regular Maintenance of Kerb Paver Machine is Essential?
A kerb paver machine operates under continuous stress due to high workloads, exposure to abrasive materials, and constant mechanical movement. Without routine maintenance, critical components such as the hydraulic system, augers, and Moulds can deteriorate, leading to inefficiencies and costly breakdowns. Regular servicing ensures consistent kerb formation, reduces downtime, and extends the lifespan of key parts, improving overall project efficiency.
- Prevents Unexpected Breakdowns Timely inspections help detect early signs of wear, reducing the risk of sudden failures.
- Enhances Hydraulic System Efficiency Clean hydraulic fluid and leak-free hoses maintain pressure consistency for smooth operation.
- Improves Kerb Quality Well-maintained augers and Moulds ensure precise shaping and uniformity in kerb construction.
- Reduces Repair Costs Addressing minor issues early prevents expensive repairs and component replacements.
- Optimizes Fuel and Energy Efficiency A well-maintained engine and clean filters improve fuel consumption and overall machine performance.
- Extends Equipment Lifespan Regular lubrication and part replacements reduce wear, keeping the machine functional for longer.
- Minimizes Downtime Scheduled maintenance ensures continuous operation without unexpected stoppages.
Common Issues Faced Without Proper Kerb Paver Machine Maintenance
Before discussing essential maintenance tips, it’s important to understand the common failures caused by poor upkeep.
1. Mechanical Failures and Downtime
Unlubricated bearings, loose fasteners, and worn-out moving parts contribute to unexpected breakdowns, reducing machine productivity.
2. Hydraulic System Malfunctions
Contaminated or low hydraulic fluid affects pressure consistency, leading to uneven kerb extrusion and slower operation.
3. Uneven Kerb Formation
Damaged augers, worn molds, or inconsistent material flow can result in kerbs with irregular shapes or poor structural integrity.
4. Increased Component Wear
Continuous exposure to harsh environmental conditions and improper cleaning accelerates wear on the hopper, track system, and other high-contact areas.
Addressing these risks through maintenance of kerb paver machine ensures consistent output and reduces long-term repair costs.
Key Maintenance Tips for Kerb Paver Machine
A kerb paver machine consists of multiple interconnected systems, each requiring specific maintenance to function optimally. Wear-intensive components like augers, moulds, and hydraulic parts demand regular attention to prevent performance decline. Neglecting key maintenance tasks can lead to misalignment, irregular kerb formation, and increased strain on the engine and transmission. Implementing a structured maintenance routine helps maintain efficiency, prevents premature failures, and ensures consistent output on every project.
1. Cleaning to Prevent Material Build-up
Cleaning the machine after each use is essential for preventing hardened concrete from blocking critical components like the hopper, augers, and moulds. Leftover material can build up over time and affect the smooth flow of fresh concrete, resulting in inconsistent kerb formation and potential machine damage. Regular cleaning also ensures that parts remain free from concrete residues that could cause wear or corrosion.
- Remove residual concrete from the hopper and augers after each use.
- Clean moulds thoroughly to prevent material build-up that could impact kerb quality.
- Use a high-pressure washer to clear debris from moving parts, ensuring smooth operation.
2. Lubrication of Moving Parts
Proper lubrication ensures that all moving parts in the machine operate efficiently and reduces friction that can lead to wear. Applying the right amount of lubricant to pivot points, chains, and bearings prevents premature degradation of these components, which are essential for the machine’s functionality. Regularly lubricating key areas also reduces the risk of mechanical failure and downtime, leading to more consistent performance.
- Apply grease to the pivot points, chains, and bearings according to the manufacturer’s guidelines.
- Use high-quality lubricants to avoid premature wear and ensure smooth operation.
- Check for any dried-out grease or excess accumulation that may indicate improper application.
- Inspect the lubrication system regularly to ensure adequate flow to all moving parts.
3. Hydraulic System Inspection
The hydraulic system is responsible for several critical functions in the kerb paver machine, including controlling the augers and moulds. Maintaining the hydraulic system is essential to ensure smooth, consistent operation. If the hydraulic fluid is contaminated, low, or leaking, it can cause issues such as uneven kerb formation or slow operation. Regular inspection and maintenance of the hydraulic system help prevent costly repairs and downtime.
- Keep hydraulic fluid at optimal levels to maintain proper system pressure.
- Check hoses and fittings for leaks that may lead to performance issues.
- Replace hydraulic filters at recommended intervals to prevent fluid contamination.
- Test hydraulic pumps and cylinders for proper operation to avoid uneven concrete flow.
4. Monitoring Wear on Moulds and Augers
Moulds and augers are key components in shaping and extruding concrete. Over time, these parts can wear down due to the constant friction and stress of moving heavy materials. Monitoring their condition and replacing worn-out parts when needed ensures that kerb formation remains precise and efficient. It’s crucial to inspect these components regularly to avoid issues that can compromise the quality of the kerb or cause mechanical breakdowns.
- Inspect moulds for cracks or excessive wear that could lead to poor kerb alignment.
- Replace augers if they show signs of wear or damage, ensuring consistent material flow.
- Regularly check auger blades for sharpness and signs of corrosion.
- Ensure all replacement parts are manufacturer-approved to maintain machine integrity.
5. Securing Bolts and Fasteners
Loose or improperly secured bolts and fasteners can cause the machine’s components to misalign during operation, leading to issues such as uneven kerb formation or mechanical breakdowns. Regularly checking and tightening these fasteners ensures that the machine runs smoothly and maintains structural integrity. It also helps to prevent any parts from becoming dislodged or causing damage to the machine or surrounding infrastructure.
- Tighten bolts and fasteners in high-vibration areas to prevent misalignment.
- Inspect tracks and chassis bolts regularly for signs of wear or loosening.
- Check the tightness of the bolts on the auger system to avoid slippage during operation.
- Ensure the chain tension is adjusted correctly to prevent operational inconsistencies.
- Tighten any loose parts that may affect the overall machine performance.
6. Engine and Fuel System Maintenance
The engine is the heart of the kerb paver machine, and keeping it in optimal condition is crucial for consistent performance. Regular maintenance, such as changing the oil, replacing filters, and checking the fuel system, ensures the machine runs smoothly and efficiently. A well-maintained engine improves fuel efficiency, reduces the likelihood of breakdowns, and extends the machine’s lifespan.
- Change engine oil and replace filters at recommended intervals to keep the engine running smoothly.
- Use clean, high-quality fuel to avoid clogging and system contamination.
- Inspect belts, hoses, and air filters regularly for wear, cracks, or blockages.
- Ensure proper fuel and air circulation to avoid engine overheating.
- Check for any fuel leaks that may lead to performance issues or safety hazards.
7. Proper Storage to Prevent Environmental Damage
Proper storage is a critical part of machine maintenance, especially when the machine is not in use. Exposing the kerb paver machine to harsh weather conditions, moisture, or dust can cause premature corrosion and wear on essential components. Storing the machine in a clean, dry, and sheltered space helps protect its parts and keeps it in good working order for future use.
- Store the machine in a dry, sheltered area to protect against weather-related damage.
- If the machine will be idle for an extended period, drain the fuel and hydraulic fluids.
- Cover exposed components, such as the engine and electrical parts, to protect them from dust and moisture.
- Ensure the storage area is free from excessive humidity and extreme temperatures that can cause deterioration.
8. Adhering to the Manufacturer’s Service Schedule
Following the manufacturer’s service schedule is vital for keeping the kerb paver machine in top condition. These schedules provide a timeline for routine inspections, part replacements, and overall machine assessments. Staying on top of the recommended maintenance intervals helps identify potential issues early, preventing more expensive repairs and ensuring the machine operates at peak efficiency.
- Follow the recommended service intervals for all inspections, oil changes, and filter replacements.
- Schedule professional servicing at regular intervals to ensure all systems are functioning properly.
- Address minor issues early to avoid them turning into major failures.
- Keep a record of all maintenance activities and repairs for reference and future servicing needs.
Putting it together
Regular maintenance ensures your kerb paver machine continues to perform at its best, preventing costly downtime and extending its operational life. Staying on top of cleaning, lubrication, and system checks will keep all components working efficiently, resulting in smoother operations and better kerb quality. Addressing minor issues early can save you from major repairs down the road.
For expert advice or help with your machine’s maintenance, don’t hesitate to contact us at info@aaspaequipment.com we’re here to support you every step of the way.