Importance of Machine Laid Kerbs in BRTS Corridors in BRTS Corridors
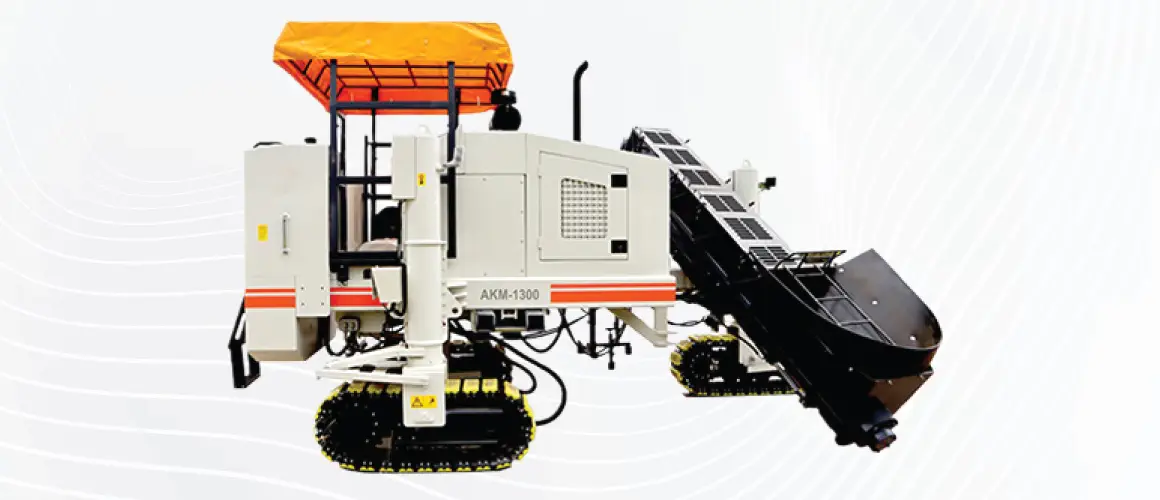
Kerbs define lane boundaries, guide drainage, and ensure structural stability across the corridor. With the increasing push for quality and speed in road infrastructure, machine laid kerbs are becoming the preferred choice in BRTS development. This blog explores why they matter and how they enhance the overall performance of BRTS corridors.
What is machine laid kerbs?
Machine laid kerbs are created using specialized kerb laying machines that extrude pre-mixed concrete or asphalt into a continuous kerb line. Unlike traditional methods that rely heavily on manual labor and brick-by-brick placement, these machines follow a guided path and lay kerbs with uniform shape, height, and alignment.
They are used to create straight or curved boundaries quickly, consistently, and with minimal margin of error. In the context of BRTS corridors, where every millimeter of alignment counts, this method ensures long-lasting and visually clean results.
Why kerbing is essential in BRTS infrastructure?
BRTS corridors function in a high-traffic, high-speed setting where safety, lane discipline, and proper segregation of spaces are non-negotiable. Kerbs in such setups:
- Define the edges of the dedicated bus lane.
- Act as a barrier between vehicular and pedestrian/cycle lanes.
- Support efficient drainage by directing surface water.
- Protect pavements, medians, and station infrastructure from vehicular impact.
- Enhance the overall look and organization of the corridor.
Manual kerbing often fails to meet these requirements in terms of uniformity and durability. That’s where machine laid kerbs bring a significant upgrade.
Key Challenges with traditional kerb laying
Manual kerbing comes with several downsides, especially in high-performance transport infrastructure like BRTS:
- Varying height and alignment across the stretch.
- Labour-intensive processes prone to delays and errors.
- Poor compaction leading to weak joints and faster wear.
- Longer downtime on site, causing traffic disruption.
- High cost of maintenance and frequent repairs.
Key benefits of machine laid kerbs in BRTS corridors
1. Consistent alignment and accuracy
Machine laid kerbs follow a fixed line and slope, maintaining exact alignment throughout the stretch. This is especially important in BRTS corridors where inconsistent kerb height or layout can disrupt bus movement and create safety hazards.
2. Faster execution with reduced manpower
Kerb laying machines can complete long stretches in much less time compared to manual methods. This is beneficial for live road projects where minimal traffic disruption is a priority. Fewer workers are needed, and the process becomes less prone to human error.
3. Stronger structural finish
These machines use vibration and compaction during laying, resulting in denser kerbs with stronger bonding. This helps the kerbs resist shifting or cracking even under heavy loads—ideal for areas with constant bus movement and occasional impact from vehicles.
4. Uniform slope for effective drainage
Water logging is a common issue in urban roads. Machine laid kerbs provide a steady and accurate gradient, which helps direct surface runoff toward designated drains. This prevents water accumulation that can weaken the road base and reduce safety.
5. Clean and professional finish
Public transport corridors are high-visibility areas. Machine laid kerbs give a neater finish, making the corridor more visually organized and safer for all users—especially when lane boundaries are clearly defined for pedestrians, cyclists, and buses.
6. Reduced maintenance in the long term
With better compaction, tighter joints, and consistent shape, these kerbs tend to last longer without the need for frequent repairs. This saves both time and money on maintenance contracts and reduces future lane closures.
Applications beyond just kerb alignment
Machine laid kerbs are also being used in other parts of the corridor, such as:
- Median separation between BRT lanes and mixed traffic.
- Island dividers near pedestrian crossings and stations.
- Approach zones to bus stations for guided entry and exit.
Their ability to maintain shape, line, and height makes them useful in multiple configurations across the corridor design.
With urban infrastructure timelines becoming tighter, these challenges make the manual method less suitable for critical applications.
Conclusion
Machine laid kerbs are not just a modern convenience—they are a functional upgrade that supports the core objectives of BRTS corridors: safety, speed, and structural efficiency. From ensuring alignment and drainage accuracy to reducing maintenance overhead and project delays, they offer tangible benefits across planning, execution, and long-term operations.
For urban infrastructure developers, municipal contractors, and EPC agencies looking to streamline kerb construction in BRTS or urban road projects, shifting to machine laid kerbing isn’t just an option—it’s a proven path to better performance.
To know more about kerb laying equipment, specifications, or project support, get in touch with our technical team at info@aaspaequipment.com. We’ll be happy to assist you with machine recommendations, custom configurations, and pricing tailored to your project needs.