Safety Tips for Handling Asphalt Drum Mix Plant: A Comprehensive Guide
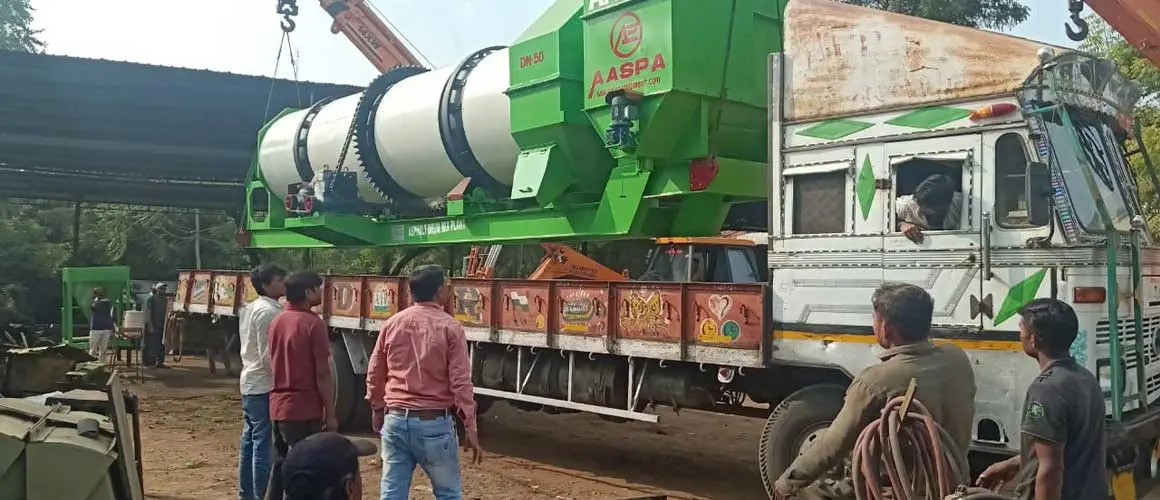
In this detailed guide, we will shade lights on the safety tips for handling an asphalt drum mix plant.
1. Wear Appropriate Personal Protective Equipment (PPE)
Working with asphalt drum mix plants exposes operators to dust, fumes, and high temperatures. Proper personal protective equipment (PPE) is crucial:
- Safety Helmets: Protects against potential falling debris.
- Heat-resistant Gloves and Clothing: Essential for avoiding burns, especially around the mixing drum and conveyors.
- Protective Eyewear and Face Masks: Shields your eyes and respiratory system from asphalt fumes, dust, and particles.
- High-visibility Vests and Steel-toed Boots: Ensure you are seen and protected from impact injuries in high-risk zones.
Wearing PPE minimizes exposure to hazards and prepares you for unexpected situations.
2. Inspect Equipment Before Operation
Routine inspections are essential to identify wear and tear, loose parts, or damage that may compromise safety. Start each day with a thorough equipment check, including:
- Belts, Chains, and Pulleys: Examine for wear and proper tension, ensuring they function smoothly.
- Mixing Drum Condition: Look for cracks, dents, or rust spots that might worsen under pressure.
- Burner Alignment and Nozzles: Confirm proper alignment and cleanliness, as misaligned burners can lead to overheating or unplanned shutdowns.
- Electrical and Control Panels: Check for exposed wires or signs of overheating that may indicate electrical issues.
Identifying potential issues early helps prevent malfunctions and reduces downtime.
3. Follow Manufacturer’s Guidelines
Each asphalt drum mix plant comes with specific operational guidelines from the manufacturer. Familiarize yourself with these instructions and always refer to them when in doubt:
- Start-up and Shutdown Procedures: Manufacturers often outline step-by-step processes that are optimized for safety and efficiency.
- Load and Temperature Settings: Use recommended material loads and temperature ranges to avoid overheating or clogging the mixing drum.
- Maintenance Schedule: Keep a log for regular maintenance activities as prescribed in the manual, ensuring equipment remains in peak condition.
These guidelines are designed to minimize risks, so following them is crucial for safe operation.
4. Maintain a Clean and Organized Work Area
A cluttered workspace increases the risk of accidents, especially with heavy machinery like an asphalt drum mix plant. Ensure that:
- Tools and Equipment are Properly Stored: Avoid leaving tools around the plant, as they can become hazards if accidentally picked up by moving parts.
- Pathways are Clear: Workers should have easy access to exit routes and safety stations without navigating obstacles.
- Regular Housekeeping is Observed: Remove excess asphalt, dust, and other debris from the plant area. A buildup can pose fire hazards and cause operational inefficiencies.
Keeping the workspace clean enhances safety and efficiency.
5. Be Cautious Around High-Temperature Areas
High-temperature zones, especially near the mixing drum and burner, pose burn risks. Implement these precautions to handle hot areas safely:
- Allow Equipment to Cool Before Maintenance: Wait for the plant to cool down before conducting any repairs or adjustments.
- Use Insulating Barriers and Shields: Where possible, install barriers around high-heat areas to prevent accidental contact.
- Set Up Warning Signs: Clearly label hot surfaces and areas to alert personnel and visitors of burn risks.
Awareness and caution around high-temperature areas reduces the likelihood of burn injuries.
6. Ensure Proper Training and Supervision
Operators need specialized training to work with asphalt drum mix plants safely. Ensure all staff involved in the operation undergo rigorous training, including:
- Operating Procedures and Controls: Familiarize operators with plant controls, safety mechanisms, and emergency shutdown procedures.
- Emergency Response Training: Staff should know how to respond in cases of fire, equipment malfunction, or injury.
- Routine Safety Drills: Conduct drills that simulate potential hazards, helping workers stay prepared.
Qualified personnel who understand the equipment and safety procedures are a key factor in accident prevention.
7. Use Proper Lockout/Tagout (LOTO) Procedures
Lockout/Tagout (LOTO) procedures are critical when performing maintenance on an asphalt drum mix plant. These practices ensure that equipment cannot be accidentally energized during repairs:
- Shut Down the Plant Completely: Ensure the plant is fully powered down before beginning maintenance work.
- Secure Power Sources: Disconnect electrical and pneumatic energy sources, tagging them to prevent accidental reconnection.
- Communicate with Staff: Inform all personnel that maintenance is in progress and provide clear signage.
LOTO procedures protect against accidental startups, significantly improving maintenance safety.
8. Be Mindful of Exhaust and Fumes
Asphalt plants release fumes and gases that can be hazardous if inhaled in high quantities. To minimize exposure:
- Work in Well-ventilated Areas: Ensure good airflow around the plant, particularly in enclosed spaces.
- Install Exhaust Fans and Air Purifiers: Use ventilation systems to reduce fume concentrations.
- Limit Exposure Duration: Rotate staff and allow breaks to reduce prolonged exposure to potentially harmful fumes.
Taking steps to manage fumes is essential for long-term respiratory health.
9. Monitor Weather Conditions and Environmental Factors
Asphalt plants are often exposed to outdoor conditions, so monitoring weather and environmental changes is crucial:
- Rain and Moisture Precautions: Rainwater can cool the drum too quickly or create steam bursts when in contact with hot asphalt. Cover exposed components and avoid processing during heavy rain.
- Temperature Adjustments: Extremely cold weather can impact the plant’s heating systems, requiring extra time to reach optimal mixing temperatures.
- Wind Awareness: Strong winds can affect burner flame stability and fume dispersal, so adjust operations accordingly.
Environmental awareness ensures smoother operations and helps prevent potential accidents related to weather.
10. Practice Continuous Monitoring During Operation
During operation, continuous monitoring is key to catching potential issues before they escalate. Designate a responsible individual to oversee:
- Temperature and Pressure Gauges: Regularly check readings to ensure they remain within safe limits.
- Material Flow and Mixture Consistency: Verify that materials are moving through the plant smoothly and maintaining the desired consistency.
- Noise Levels: Unusual sounds can signal mechanical problems, so encourage operators to report any strange noises immediately.
Real-time monitoring allows quick adjustments, minimizing risks and maintaining production quality.
Ending note
Safety is at the heart of efficient asphalt plant operations, and with these tips, you’re set to create a safer workspace.
Got questions or need tailored advice? The team at Aaspa Equipment is just an email away! Reach out anytime at info@aaspaequipment.com — we’re here to help.